The stator and rotor are key components of a colloid mill. They work together to facilitate the milling or grinding process.
1. Stator
The stator is the stationary part of the colloid mill, serving as a fixed anchor for the milling process. It has a series of specially designed grooves or teeth on its inner surface. Interacting with the rotor, the fixed gear creates a shearing effect on the material passing through the mill. In addition, the design of the stator significantly influences the final particle size of the product. The size and configuration of the stator’s internal elements determine the level of shearing and grinding applied to the material.
2. Rotor
The rotor is the rotating part of the colloid mill, which usually has a cylindrical or conical structure that fits within the fixed teeth. The rotor has various types of blades, teeth, or pins. As the rotating gear rotates, it generates a high-speed movement within the colloid mill, creating a shearing effect as it interacts with the fixed gear. Additionally, the gap between the rotating and fixed teeth can be adjusted to control the particle size produced during the milling process.
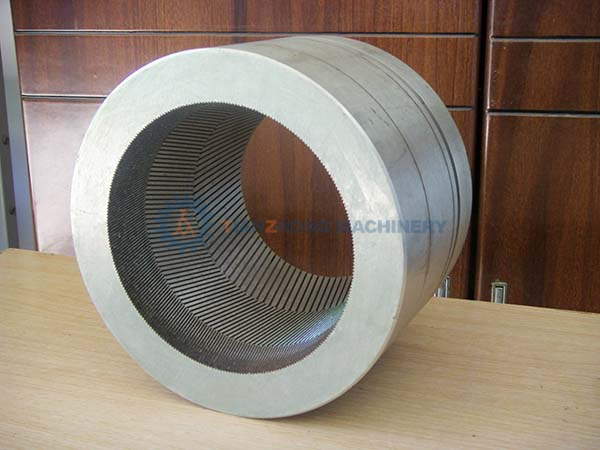

Stator and Rotor for Sale
Tianzhong Machinery offers various options of stator and rotor, from both tooth design, fineness, and materials, tailored for diverse materials and applications.
Materials
1. Stainless Steel with Vacuum Quenching: The Vacuum quenching process enhances the material’s mechanical properties by thorough and controlled cooling, improving its resistance to wear and tear;
2. Stainless Steel with QPQ Process: The QPQ treatment further refines the surface of the rotor, enhancing hardness, wear resistance, and corrosion resistance;
3. Alloy Coated Stator and Rotor: Alloy coating is versatile and adaptable to different materials, which enhances the rotor’s resistance to abrasion;
4. Diamond Coated Stator and Rotor: This coating offers exceptional hardness and wear resistance. Its superior durability and longevity significantly improves the rotor’s performance under extreme conditions.
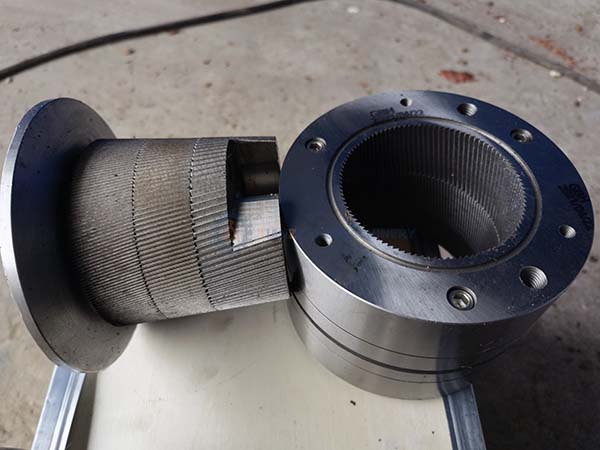
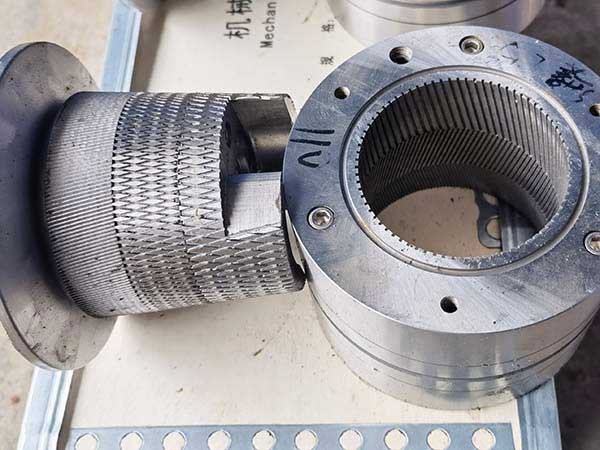
Alloy Coated Stator and Rotor
Alloy coating is a hardened layer of tungsten carbide coating, which is applied though thermal spray coating process, to enhance the wear resistance and extend lifespan. The alloy coated stator and rotor is a cost-effective solution for clients with high wear rates.
Chemical Composition: Tungsten/W: 84%; Chromium/Cr: 4%; Cobalt/Co: 10%; Carbon/C: Remaining
Utilizing high-velocity oxygen fuel (HVOF) spraying, cobalt-based tungsten carbide alloy powder is applied, achieving a remarkable hardness of HRC71-75, high-temperature resistance up to approximately 850°C, porosity less than 1%, and a bonding strength exceeding 75MPA. This coating offers stators and rotors exceptional wear resistance, corrosion resistance, high-temperature resistance, and oxidation resistance, extending the service life by 2-10 times.
Below is a table comparing the materials mentioned above.
Materials | Stainless Steel with Vacuum Quenching | Stainless Steel with QPQ Process | Alloy Coated Stator and Rotor | Diamond Coated Stator and Rotor |
Hardness | HRC45 | HRC65 | HRC75 | Mohs Hardness 10 |
Service Life | 1 Unit (assumed to be 1 unit) | 3 Units | 5 Units | 15-20 Units |
Teeth Design of Stator and Rotor
At Tianzhong Machinery, there are various teeth designs of stator and rotor for different materials, including V-shaped design, diomand design, etc. We will suggest you the suitable teeth design according to the materials you will process.
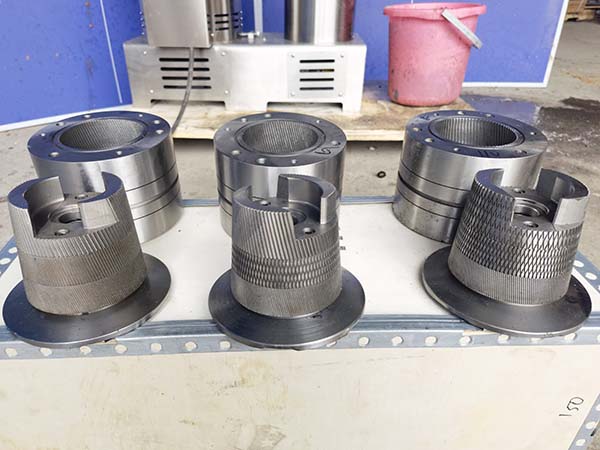
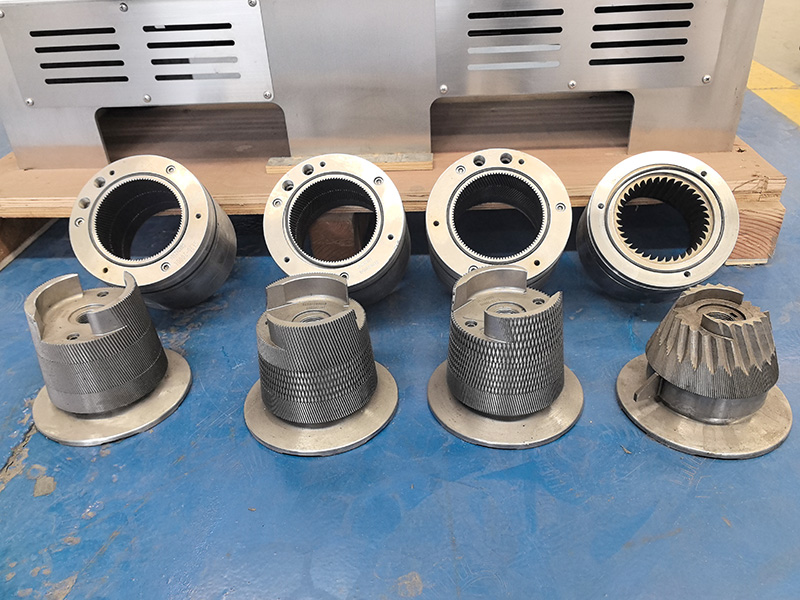
Conclusion
As a reliable colloid machine supplier, Tianzhong Machinery offers various stators and rotors to choose from. Our experienced team will provide you suitable design and material according to the applications of your colloid mill. No matter what materials you will process, nuts, meet or fruits and vegetables, you will have the most cost-effective solutions. Welcome to contact us for more details!